Could Compressed Air Leaks Be Impacting Your Bottom Line?
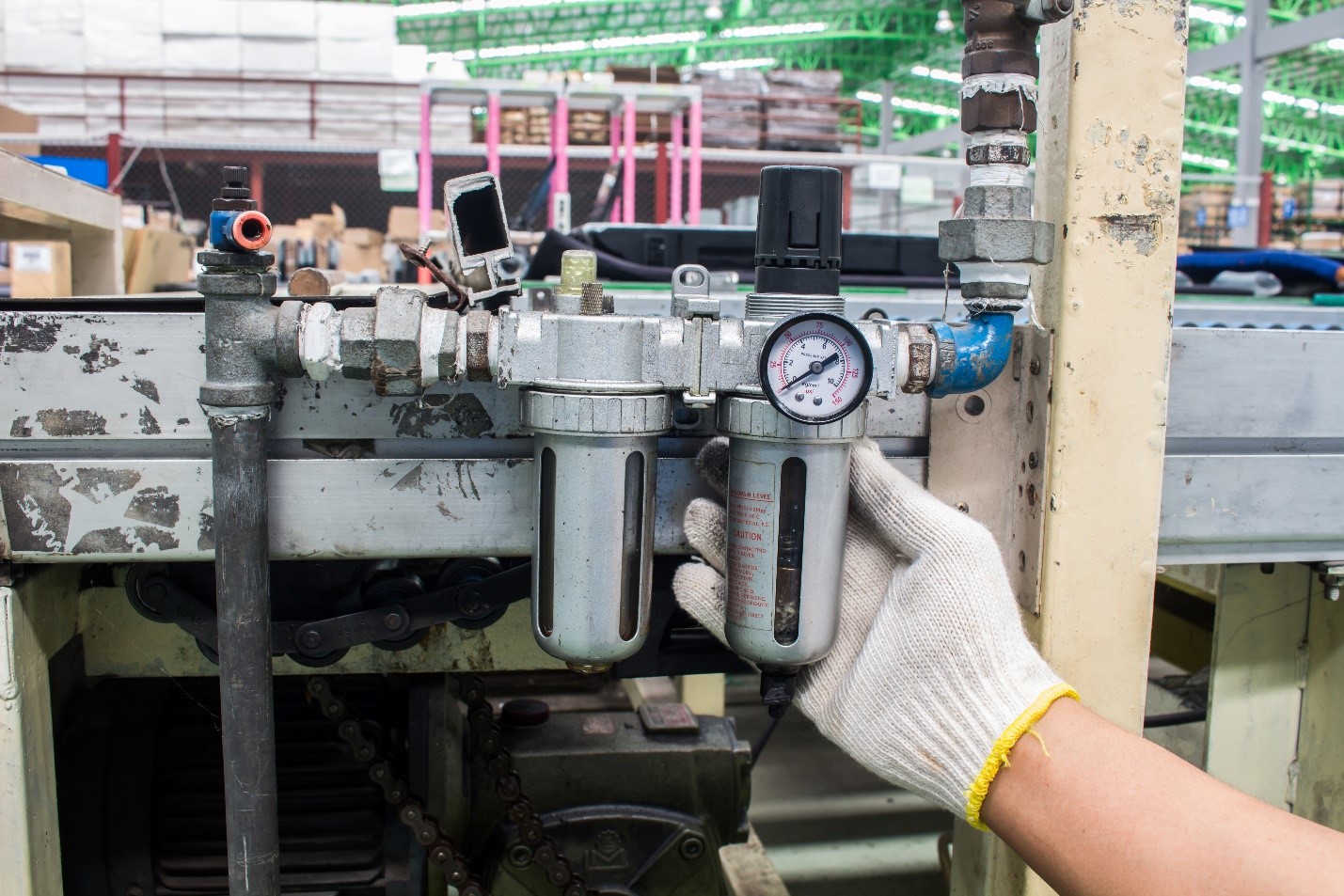
Leaks are a significant source of wasted energy in compressed air systems and if left unchecked, can account for half of a system's operating capacity or more. Since these leaks don't fix themselves, they are present 100% of the time during operating hours. Ultimately, compressed air leaks hit a company's bottom line when you look at the operational costs associated with them. Here's what to know about this type of air leak, how to identify these leaks and most important, how to fix them.
Compressed Air is Expensive
Not only is compressed air expensive but it's likely your most expensive source of power. A compressor turns electrical power into stored mechanical energy (work in) and the end use turns the stored mechanical energy into work (work out). The efficiency of a typical compressed air system is about 13%.
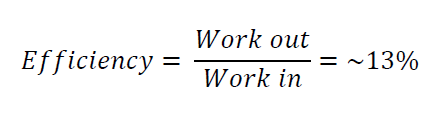
Know Your Unit Costs of Compressed Air
The cost of one cubic foot per minute (cfm) of compressed air is highly dependent on a system's operating hours and the compressor controls. Inlet modulating compressors can make one more cfm at a very minimal cost while variable-speed drive compressors save money on every cfm saved. On/off compressors have the highest incremental costs and savings. You can determine flow and cost by measuring compressor energy use over time but a good rule of thumb is $100 per cfm.
Identifying Air Leaks
Common places to find air leaks are quick-connect fittings, push-to-connect fittings, cuts or pinholes in the hoses, threaded fittings and pneumatic tools. Another important area of focus for leak detection is the "dirty thirty", which is the last run of compressed air piping that connects the end use pneumatic equipment to the compressed air header. This piping is usually 30 feet long and often has a significant drop in operating pressure (psi).
Two places to not search for leaks are the internal seals of the air cylinders and the main header pipes. Air cylinder internal seals do leak but the cost to fix them will likely outweigh the ongoing costs of the leak. Main header leaks are uncommon but when they do happen, they are usually huge leaks that impact the ability to even run the air compressor and entail a much larger fix than just sealing an air leak.
Trying to identify air leaks using only your senses is very difficult. Air is invisible so leaks cannot be seen, and leaks are very hard to hear in production areas where there is significant background noise. Today's industry standard and best practice for air leak detection is to use ultrasonic equipment.
Quantifying Air Leaks
Ultrasonic leak detectors pick up on the high-frequency noise generated from high pressure gas (air) escaping through a crack or hole and record a decibel reading. The decibel reading is then used along with the system operating pressure to quantify the air leak in cfm. Companies such as UE Systems, Inc. have applications which allow for users to input recorded decibel readings and then generate a comprehensive report that includes the estimated cfm loss, up-to-date cost avoidance and greenhouse gas reductions.
How to Fix Leaks
According to Ron Marshall from the Compressed Air Challenge, eliminating an air leak can be as simple as tightening a connection or as complex as replacing faulty equipment such as couplings, fittings, pipe sections, hoses, joints, drains and traps. Most of the time leaks are caused by faulty or improperly applied thread sealant. Choosing high-quality fittings, disconnects, hoses and tubing, and installing them properly with appropriate thread sealant is very important in avoiding future leaks.
Also, non-operating equipment can be an additional source of leaks. Equipment no longer in use should be isolated with a valve in the distribution system.
Project Example
In fall 2020, a SWEPCO Arkansas customer took on an energy efficiency project to identify and fix compressed air leaks in its manufacturing facility. The facility has over 350 horsepower of air compressors and operates at a pressure of 95 psig. Over the course of the project, the team identified 118 different leaks, representing ongoing losses of 322 cfm. The most common places where air leaks were found in this facility were in quick-connect fittings, filter bowls and hose clamps.
After repairing all the identified leaks, the customer expects to save an estimated 231,544 kWh in annual energy use. This equates to approximately $18,523 in annual utility savings, assuming an average cost of $0.08 per kWh. The overall cost of the project resulted in a simple payback period of approximately 1.25 years.
SWEPCO Offers Incentives to Repair Compressed Air Leaks
The SWEPCO Arkansas Commercial & Industrial Energy Efficiency Pathway and the SWEPCO Texas Commercial & Industrial Energy Efficiency Programs provide energy efficiency incentives to eligible customers with peak kW usage of 100 kW or more. Incentives are available for energy efficient upgrades on lighting, HVAC equipment, compressed air systems and other equipment.
In the above project example, by utilizing SWEPCO's Compressed Air Leak Detection and Repair Promotion, the customer received a sufficient amount of SWEPCO energy efficiency incentives to reduce the simple payback period from 1.25 years to 0 years. If you would like to learn more about a potential compressed air leak project at your facility or if you are interested in learning more about SWEPCO's Commercial & Industrial Energy Efficiency Programs in general, please contact:
Arkansas
Greg Perkins
gaperkins@aep.com
479-973-2435
Louisiana
Mike Nix
mrnix@aep.com
903-223-5752
Texas
Mike Nix
mrnix@aep.com
903-223-5752